Pharmaceutical manufacturing
We are helping the pharmaceutical manufacturing industry to lower water consumption and operating costs while protecting the environment.
Water Stewardship Programme
Here are some cost-effective solutions to help lower water consumption and operating costs. Companies can also avail of our free training programme - a Certification in International Best Practice Water Stewardship.
Baseline Water Footprint
This first step will help you capture a baseline of your current water usage and identify sources of risk like leakage, inability to expand production, and compliance concerns.
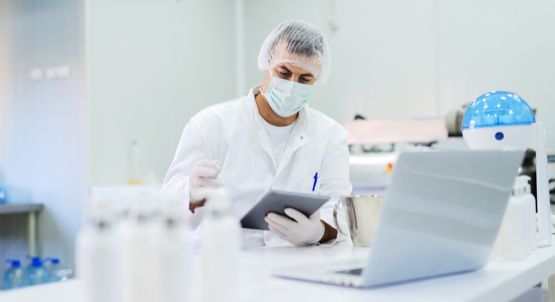
Establish a water balance for your site
A water balance provides a full picture of every water-consuming component on site and serves as the first step in uncovering hidden opportunities for savings. We propose including all flows of water into and out of the six basic categories from the water balance format; Inlet water pre-treatment, Cooling towers, Boilers, Processing (any water consuming facility which is a part of the production process), Wastewater plant (if it exists), or water effluent, Other (ash ponds in a power plant).
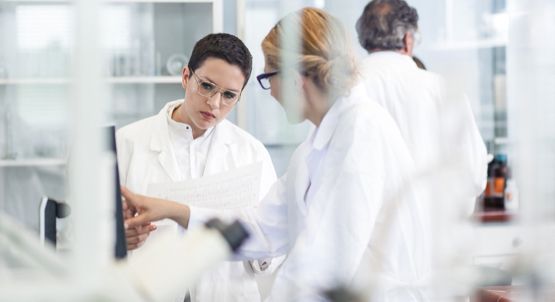
Capture water related costs
In addition to capturing related flow capacities, collecting all related costs will provide an insight into where to save money on water bills. These are the following related costs: Water use, Wastewater discharge fees, Pre-treatment technology, Energy costs associated with water use (heating, pumping, water treatment etc.), Regulatory costs (permits, compliance assessment, etc.), Costs for water management measures (staff time / resources, technology, equipment and materials)
Identify opportunities
Sources for water reuse and recycling
Based on your water balance, rank the various components by water usage and focus on the largest water users. Identify leakages and sources for waste like excess cleaning and washing.
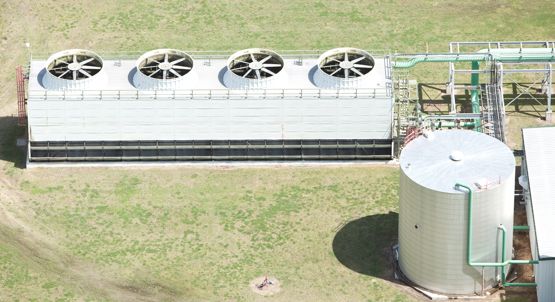
Cooling towers
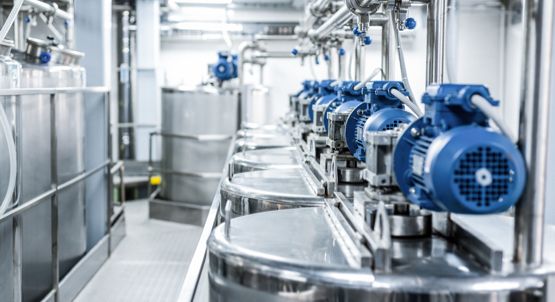
Equipment cooling
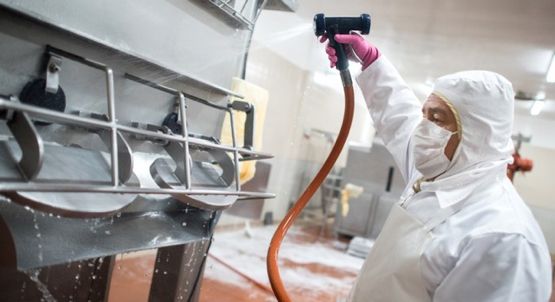
Equipment rinsing and cleaning
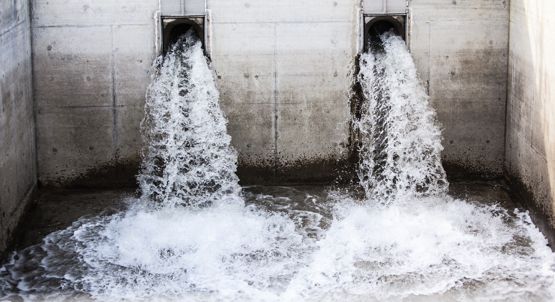
Alternative water sources
Engage stakeholders
Getting your stakeholders involved early on is essential in establishing initial buy-in, and ensuring the ongoing succcess of any water conservation campaign.
Your employees as a source for water savings ideas
- Identify process and product innovations and estimate the total effect on water savings to establish a goal.
- Establish a budget and procure funding. Outside funding and grants can be available.
- Develop a timeline for implementation and schedule periodic reviews with the water efficiency team to monitor progress.
- Develop an internal communications plan to continue engaging employees and creating awareness.
Execute and measure
Reducing your water footprint not only improves your operating performance and compliance, it also creates value for your customers and shareholders.
Ensure the economic value outweighs the cost of the project
Reducing your water footprint has several layers of value recognition. When monitoring the progree of a water project, it is recommended to capture the achieved value in all categories e.g. economic. In order to execute a water related project, the economic value has to outweigh the cost of the project. Using Steps 1-3 of the water efficiency process will allow you to compare the existing cost structure to a future state.
Operating Performance |
| Environmental Performance |
---|---|---|
Reduced consumption | + | Reduced waste |
Improved availability | + | Make use of brackish water |
Improved throughout | + | Enhanced public image |
Environmental impact goals can be managed only when they are measurable and quantifiable. Water footprint can be measured using a variety of metrics:
An Absolute Water Savings Volume - Example: 10,000 gallons per day. This metric is the simplest and most intuitive but it does not include consideration for production expansion, as future growth can result in an increased demand for water.
A Variable Metric of Water Used per Common Denominator - The most common denominators are unit production and revenue.
Examples include:
- Power - Gallons/KwHr
- Refineries - Gallons/barrel of crude oil
- Beverage - Gallons/litre of beverage
- Auto - Gallons/vehicle
- Warehouse areas - Gallons/ft2
Total Metric Tons of Wastewater Loadings - As per wastewater quality, most companies use their Corporate Sustainability Report to disclose volume of loadings in the following categories: COD, BOD, TSS and metals.
- Financial - Savings created from water projects and production expansion
- Strategic - Getting ahead of the competition by creating a more progressive sustainability policy and reporting it in the annual CSR report
- Operational - Optimised supply chain with high efficiency
- Hazard - Prevention of safety and compliance issues
Every gallon of water saved has a macro effect on the environment by being used for other purposes like residential water supply or agriculture irrigation.
Social responsibility enhances a company's image. Going beyond compliance and getting ahead of regulation can reduce time and money. Recognition comes in various forms.
“We are delighted to be the first pharmaceutical manufacturer in Ireland to participate in Uisce Éireann's Certified Water Stewardship Programme.”
Audrey Kelleher, GE Healthcare